Our ambition is to reduce the environmental impact of the food wasted by airlines.
But how big exactly is this waste, and what are the solutions to reduce it?
A. Data on food waste and meal preparations
First of all, airlines prepare an impressive quantity of food to feed their passengers. For the UAE airline company Emirates, 180,000 meals are prepared for a total of 400 flights every day. On average, Emirates thus prepares 450 meals per flight. However, most of those meals can be assumed to be loaded on regular transatlantic 10-hour flights. Indeed, it has been calculated that for 300 passengers, a company would load twice as much meals in order to satisfy their needs and offer different possibilities. The number of meals served also varies according to 1st class passengers who may choose from a larger variety of food and enjoy several meals.
The major issue we would like to stress in our work is the waste generated by this notable amount of prepared food. In 2013, more than six billion passengers travelled by plane and airplane food generated 3,5 million tons of waste. In 2016, this figure almost doubled to 5.2 million tons of waste according to the International Air Transport Association (IATA). Several reasons may explain this figure:
- travellers may not finish their meals (for various reasons, including food quality and taste)
- travellers may not wish to consume on board, or may not like the type of food served
- airlines board too much food that is then thrown out (partly due to regulations, see later)
- food served involves non-recyclable, single-use only packaging
- ...
This waste needs to be better processed since a critical amount is buried in landfills instead of being recycled. Plastics and aluminium are for instance used in the composition of wrappings. For recycling purpose, habits and equipment would also have to evolve since the tray commonly used by cabin crews do not allow for recycling. Cabin crews would also have to be trained to limit the
time used to sort waste.
B. Ecological cost of airline waste
As mentioned before, the amount of waste produced by airline food service is increasing, it is even supposed to be doubling within the next fifteen years. The following table can be used to assess the negative impact of the excess transportation of food and waste on the environment. For each 100km the amount of waste produced in 2013 has “flown”, more than two hundred tons of CO2 emissions from kerosene may have been emitted, meaning that this amount of CO2 emissions may have been prevented by a better management of food production. Later, will also be assessed the economic impact of this excess transportation.
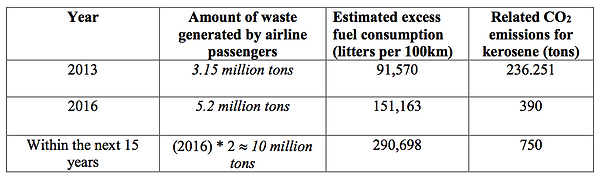
In addition, food waste is also created by delays: a 6 to 8 hours delayed flight may see all its food deemed as contaminated and have to throw everything. Improving punctuality is thus another way to lower waste.
C. Challenges and business opportunities arising from airline food waste
For airlines, the main challenge arising aside from the ecological and waste reduction challenges will also be about maintaining a good company’s image. Nowadays, people are becoming more sensitive to a business’s attitude towards the environment and its capacity to recycle and be “green”. Airlines may benefit from changing their habits and reducing their carbon footprint by recycling and reducing waste generation. However, they should not fall in the greenwashing trap, a relatively new practice defined as “a form of deceptive marketing in which a company, product, or business practice is falsely or excessively promoted as being environmentally friendly” by K. Cruger, that accounts for a situation in which companies, knowing the importance of being green will just give an image of good practices. Some initiatives should thus be considered to significantly and genuinely reduce waste. Serving excellent food catering and improving food quality may both promote the company’s image and waste reduction.
Finally, other companies may also benefit from this necessity of modifying airlines’ business models. Packaging developers like GK Thomas, which developed the “Eco-Heat Tray”, are incentivised by new business opportunities to “produce sustainable packaging solutions”. They will either focus on creating re-usable, lighter or cleaner items. Can also be mentioned Kaelis, which develops on-boards products or MTL Carton which developed the “Bold Cup” disposable line.
International catering waste (ICW) is defined as food waste which is no longer fit for human consumption coming from international transport vehicles including airlines. While airlines have increasingly undertaken initiatives to limit food waste through recycling or donation, their efforts are impeded by stringent regulations aiming at reducing the risk of disease contamination. Today, there is no comprehensive international regulations on food waste. However, members of the Convention on International Civil Aviation are required to take measures preventing the spread of communicable diseases which can limit recycling options. For instance, a number of countries, such as the US and Australia, quarantine food waste and directly incinerate it.
EU regulations are perhaps the biggest obstacle to ICW recycling or donation. The EU animalby-product regulation (1774/2002/EC) defines international catering waste as “catering (food) waste from means of transport operating internationally”. This includes food prepared in catering facilities, foods in stores or brought by passengers or the crew. It excludes sealed packets of foodstuff of non-animal origin, which are not in risk of contamination. ICW is classified as a category 1 animal by-product (unless coming from EU territory) and is as such subject to strict controls to avoid the contamination of animal diseases.
ICW must be stored in a covered, leak- proof and labelled container which is usually provided by the airport. After the ICW has been disinfected, must be disposed by:
-
incineration
-
co-incineration
-
manufacturing of derived products (biofuel)
-
burial in an authorized landfill without pre-treatment
The responsibility of disposal lies in the aircraft owner or company operating on its behalf. While the EU regulation requires every member state to ensure system of disposal, in practice infrastructures are not always adequate What is even more problematic is that under these regulations, recycling of cans, plastics, glass and paper is only possible if it has not been in contact with ICW. For instance, confectionery, crisps and nuts and drinks not containing milk can be recycled. Plastic cups which have been in contact with milk or honey cannot.
To remedy for the handcuffing regulations, airline representatives advocate reforms that would take into account already existing standards that airlines are subjected to in order to assist the recycling effort.
Despite regulatory limitations, airlines and airports are implementing programs to reduce airline food waste. One must keep in mind however, that their efforts remain fragmented and much remains to be done.
A. Airlines Commitments
Reusable materials and enhanced recycling services
Airlines try to minimize plastic waste by refining their recycling services and replacing packages and cutlery with reusable ones. In 2010, Cathay Pacific recycled 33,244 kg of aluminum cans, 29,609 kg of plastic bottles and 22,050 kg of plastic cups by sorting, reusing and recycling paper and plastics and requesting similar standards for their caterers. Virgin’s “Zero Waste to Landfill” program sets the ambitious goal of diverting 100% of its waste from landfills. Virgin has replaced its packages with reusable ones and has partnered with airport facilities to facilitate recycling and composting. In 2015, Virgin recycled 1,920 tons of waste. Air New Zealand and Qantas have replaced their cutlery with a lighter type of plastic that can be washed and re-used up to 8 times. SAS (Scandinavian Airlines) has gone even further by bettering its on-board recycling, using reusable plates, recyclable or combustible disposable packaging and locally-sourced food.
Converting waste into biofuels
Furthermore, airlines are leading initiatives to convert waste into energy. In 2014, British Airways and the American group Solena have cooperated to build a waste-to-jet-fuel plant in London to process municipal and airline waste to convert it into jet fuel. The plant can process 551, 156 tons of waste per year. British Airways has announced it will purchase the produced fuel to power its planes. A similar initiative was taken by Qatar Airways which announced in 2010 a project to produce and supply biofuel with the Qatar Science and Technology Park, Qatar Petroleum and Airbus. Today, Qatar Airways has successfully converted 6,300 litters of cooking oil into biofuels.
Donations
Some airlines, provided health regulations allow it, donate used sealed food products to homeless shelters. This is the case of United Airlines which donate unused amenities kits and leftover packets. The Australian project Oz Harvest is collaborating with Brisbane airport and Australian airlines to donate uneaten packets of food to the homeless. It is currently collecting 400 kg of food a day.
B. Airport Commitments
LIFE Zero Cabin Waste is as of today the most comprehensive model to “reduce, reuse and recycle (including energy recovery) waste collected on airplanes, and to establish the basis for other airlines to replicate this approach)” (EC Europa-Zero Cabin Waste). This is an EU initiative launched at Madrid’s Barajas airport, in cooperation with Iberia airlines, in 2014. Recoverable (plastics, cans, glass and paper) and municipal waste (including organic waste) from international and European flights will be treated. The project will be based on the training of the crew and staff, on a collection and separation protocol and on sophisticated waste processing. The project targets a waste reduction of 5% each year and a recovery of 80% of the waste diverted to landfill. It will also lower costs of disposals and create new jobs. The goal is also to create a model transferable to other airports. The model is expected to be replicated in Heathrow in 2019.
In 2017, Gatwick airport and DHL opened the first biomass burning facility to treat Category 1 waste. ICW and packaging from non-EU flights now be processed on location. The waste is converted into energy to heat the Terminal in which it is located. The site, operated by DHL, also includes a recycling facility for airport generated waste and municipal waste. It is believed that the project will save £1,000 a day in energy, waste management cost and transport for a cost of £ 35. It will also help Gatwick reach its target to recycle 85% of its waste.
The report has presented the two most detailed and advanced projects for ICW processing but many more initiatives (such as the food waste bins in the food courts of Seattle-Tacoma International Airport) are developing. ICW and airport waste has become an increasingly important area for both airlines and airports. However, it is only through a concerted effort of airlines, airports, consumers and policy makers that real progress can be achieved.